goldenchild
Well-known member
- Joined
- Aug 14, 2009
- Messages
- 1,809
So a while back I revealed to my co-worker that I was into processing and refining precious metals. He was very fascinated with the science. He eventually told me that his father actually works for a company that constructs components that use many gold plated parts and that the company would throw away parts that were excess or obsolete
So his father and his boss would take the items and sell them to someone (legally). I asked how they all determined how much to pay for the material. My co-worker told me that the guy would take small samples and have them assayed. I was a bit thrown off by this as plated material is kind of tough to assay accurately in small quantities. At least in my opinion. So I told my co-worker that his father and boss were basically riding blind and could be getting ripped off royally.
After a bunch of harassment and lecturing my co-worker finally convinced his father to give me a try. I think this finally happened because his father and boss were becoming more and more skeptical of the returns. They can actually calculate the gold content as this is true mil-spec material. The particular sample I received were center pin conductors used in satellites! The sample contained 107.3 grams of these pins. They are solid copper with what I believe to be 24k gold plating inside and out. You will see why I think this.
I was pleased the pins were non-magnetic because I knew my options were wide open on processing them. I didn't go with the obvious H2S04 cell as it was such a small sample and I wanted to get a more precise yield. I decided to go with nitric. After a quick and I mean quick incineration I threw them in a beaker with a 50/50 70% nitric/water solution. The solution got very hot and did nothing! I had to decant the acid and incinerate again. I had to really damage the outer layer to get to the copper underneath. Even after the second incineration I was only able to digest about half the pins. I got a bit impatient so after the nitric was used up I decanted and went straight to AR so sorry there are no pictures of all the foils after complete digestion.
After following standard operating procedure I gave the necessary washes and melted. The final yield for 107.3 grams of pins was .6 grams! Very impressive. The scale was actually teetering between .6 and .7 and after all done I realized I had missed about 15 pins in my pocket that were never processed. So I'm calling it .7 grams. Now I just have to compare numbers with my co-workers father. Hopefully we can strike up a deal 8)
Incoming weight
Here you can see the foils starting to float as the pins come to total digestion with nitric.
After first precipitation.
After first wash
Dried
After a bunch of harassment and lecturing my co-worker finally convinced his father to give me a try. I think this finally happened because his father and boss were becoming more and more skeptical of the returns. They can actually calculate the gold content as this is true mil-spec material. The particular sample I received were center pin conductors used in satellites! The sample contained 107.3 grams of these pins. They are solid copper with what I believe to be 24k gold plating inside and out. You will see why I think this.
I was pleased the pins were non-magnetic because I knew my options were wide open on processing them. I didn't go with the obvious H2S04 cell as it was such a small sample and I wanted to get a more precise yield. I decided to go with nitric. After a quick and I mean quick incineration I threw them in a beaker with a 50/50 70% nitric/water solution. The solution got very hot and did nothing! I had to decant the acid and incinerate again. I had to really damage the outer layer to get to the copper underneath. Even after the second incineration I was only able to digest about half the pins. I got a bit impatient so after the nitric was used up I decanted and went straight to AR so sorry there are no pictures of all the foils after complete digestion.
After following standard operating procedure I gave the necessary washes and melted. The final yield for 107.3 grams of pins was .6 grams! Very impressive. The scale was actually teetering between .6 and .7 and after all done I realized I had missed about 15 pins in my pocket that were never processed. So I'm calling it .7 grams. Now I just have to compare numbers with my co-workers father. Hopefully we can strike up a deal 8)
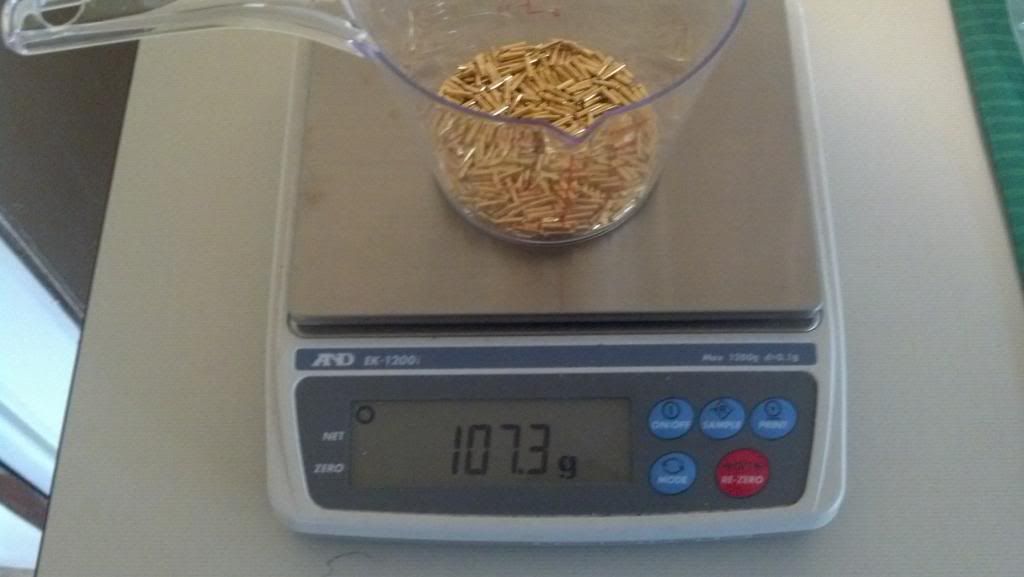
Incoming weight
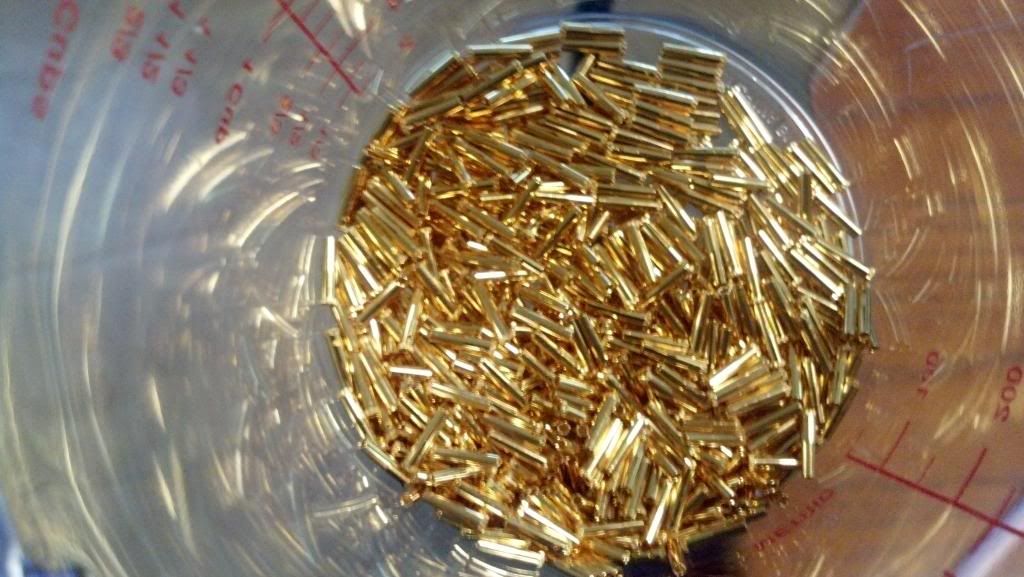
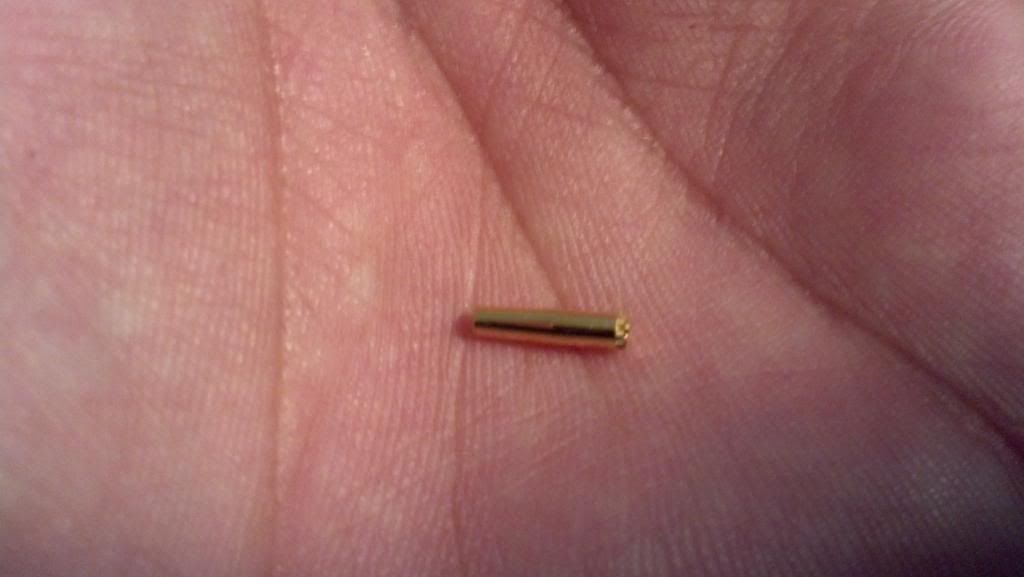
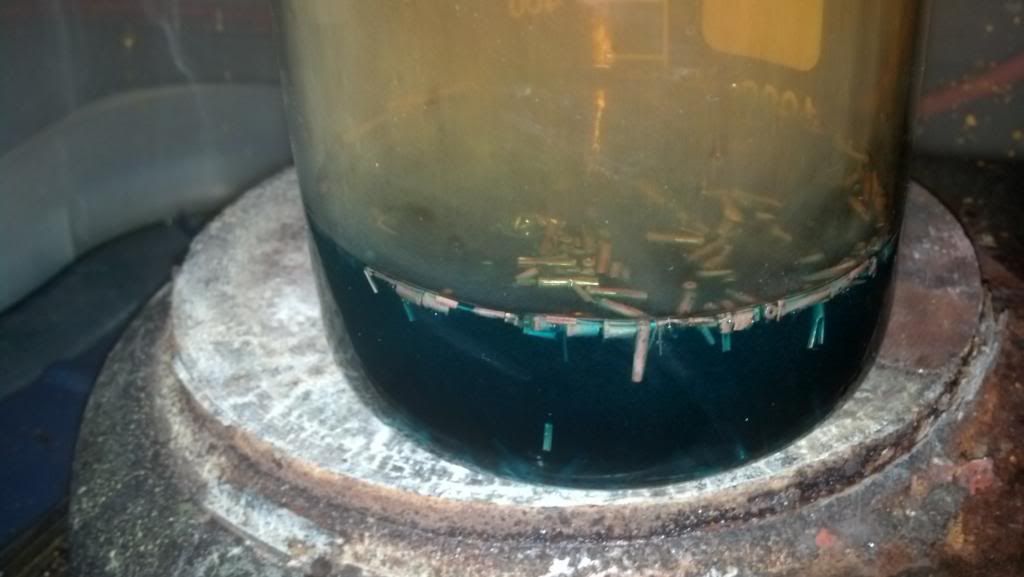
Here you can see the foils starting to float as the pins come to total digestion with nitric.
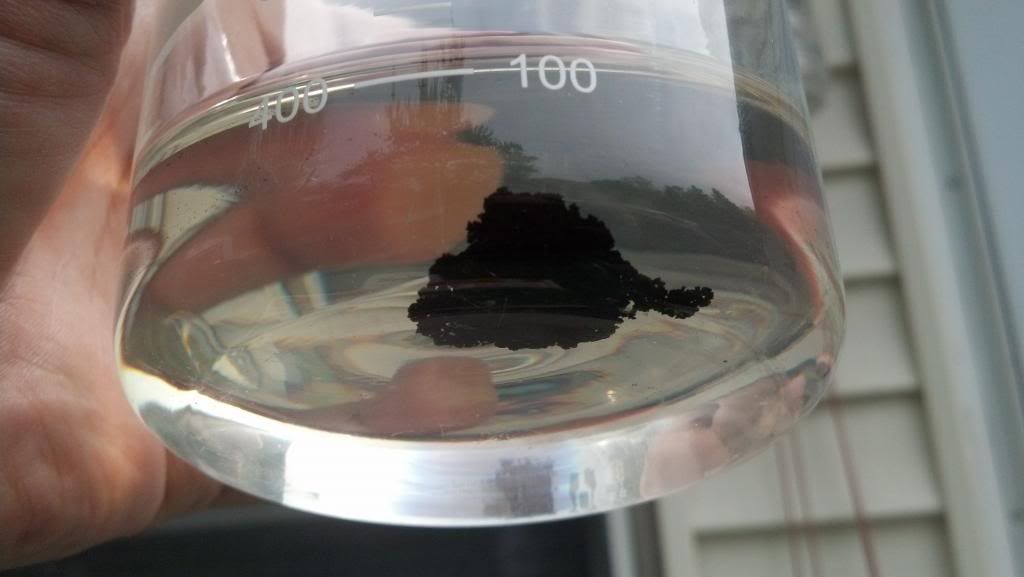
After first precipitation.
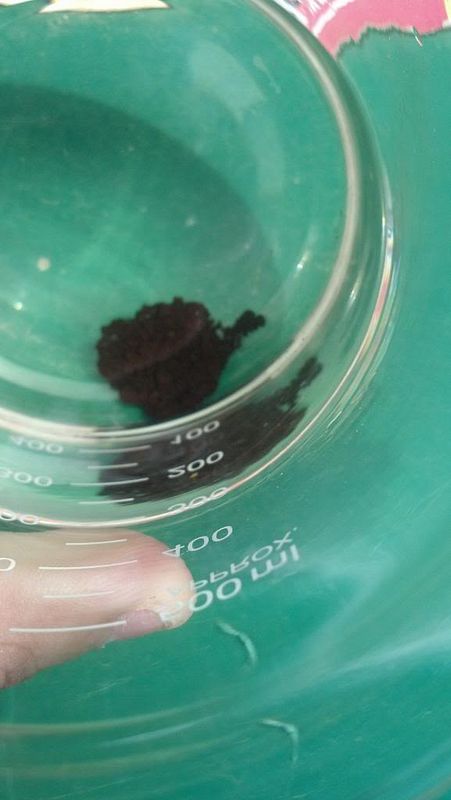
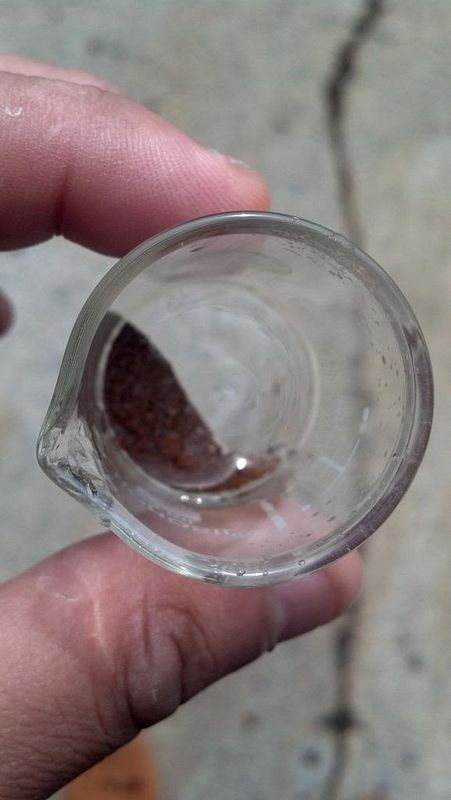
After first wash
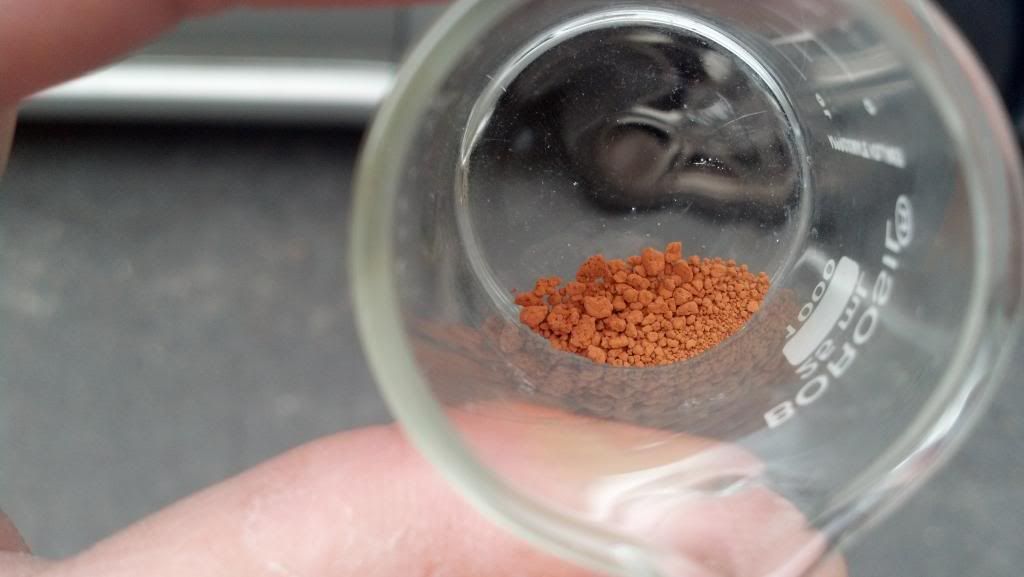
Dried
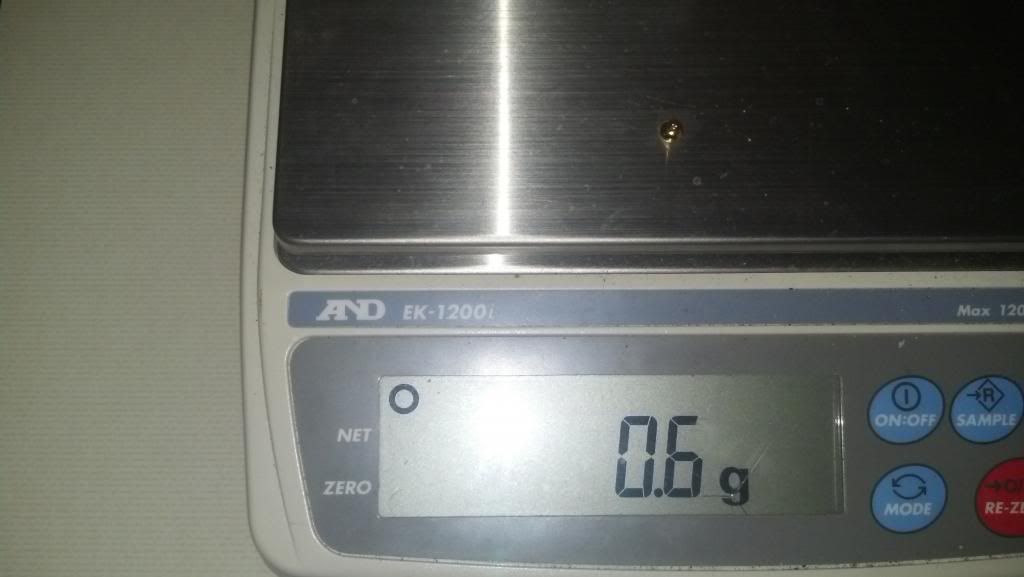
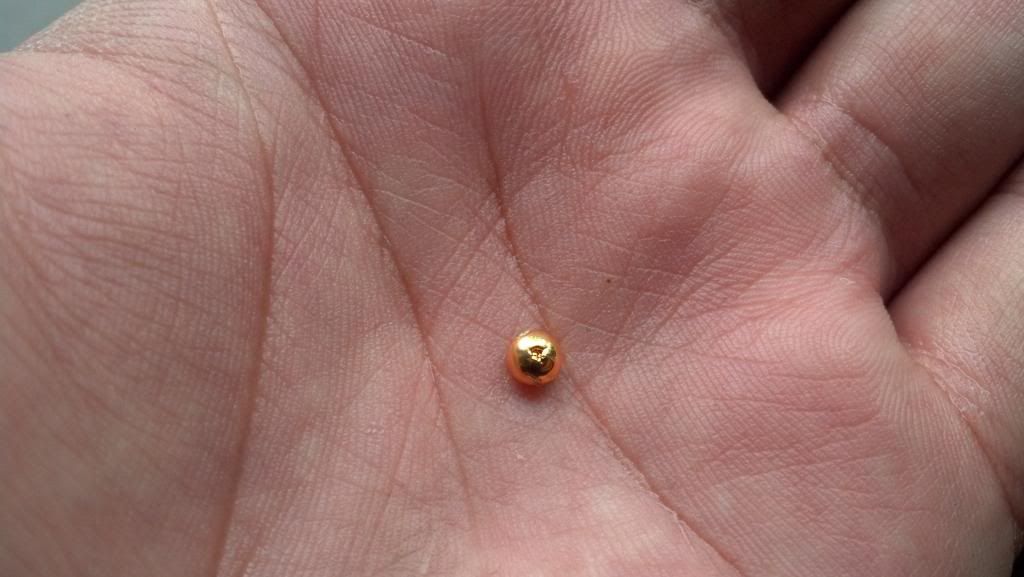