boochieboy
Member
- Joined
- May 4, 2010
- Messages
- 9
Hello everyone! I have been following these boards for a few months now (although this is my first post), and the knowledge shared on here is unbelievable. First off, thank you for the site....it is definately THE place to go for this type of information and experience. I started buying 999 silver ingots a few years ago for the simple reason that I thought it was a neat little hobby. As I have gained knowledge about precious metals, they started to interest me further, and I wanted to start learning about refining and recovery from scrap materials. I have never refined any gold or other metals, but I have collected many computers, telephones and other electronics over this past summer, and recently dismantled them all, and sold off the boards, processors etc. to refineries. As I have learned about the process, and chemicals needed to refine the metals, I have decided that it is beyond my skill and patience level to do so....but I still love my metals! My main area of interest is finding scrap sterling silver, and melting it into bullion to add to my collection of .999 ingots(unless it is worth more as a collectible piece than it's melt value). I recently went to a church sale and picked up 3 sterling demitasse spoons for $2 each (I knew they were worth much more,,,even in melt value),,,,,,they weighed in at 12, 14, and 17 grams. Not too bad getting 43 grams of sterling for $6! Anyhow, I am keeping the clamshell spoon because I like the looks of it......one has already been melted down into a button with some scrap sterling jewelry, and the other will also be melted. I am working with simple propane,,,a silica melting dish (which has been properly seasoned),,,and a wooden ingot mold I made and sooted with a candle flame. I do have one quick question though.......is the melted borax already in my melting dish enough for a 38 gram melt, or should I add more as I'm melting? Also, is there any sort of calculator or chart which would tell me how much .999 silver to add to pre-1964 US coins to bring them up from 90% to sterling? Any tips or suggestions for a novice is greatly appreciated.
1 Spoon and scrap jewelry melted into a button (uncleaned borax/flux still on it)
Spoon on left will be melted with the button and poured into wooden ingot mold
1 Spoon and scrap jewelry melted into a button (uncleaned borax/flux still on it)
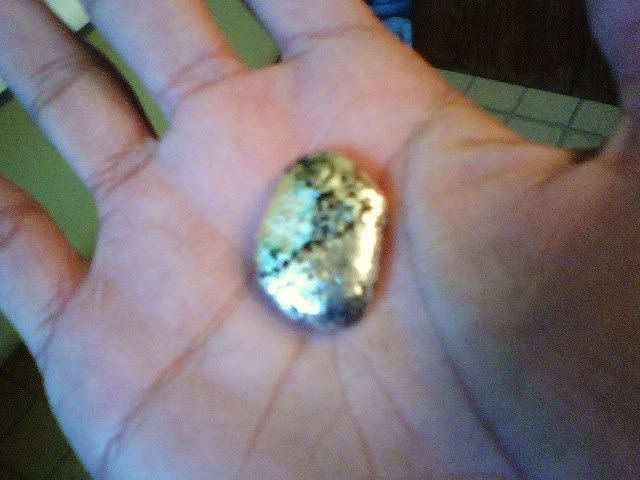
Spoon on left will be melted with the button and poured into wooden ingot mold
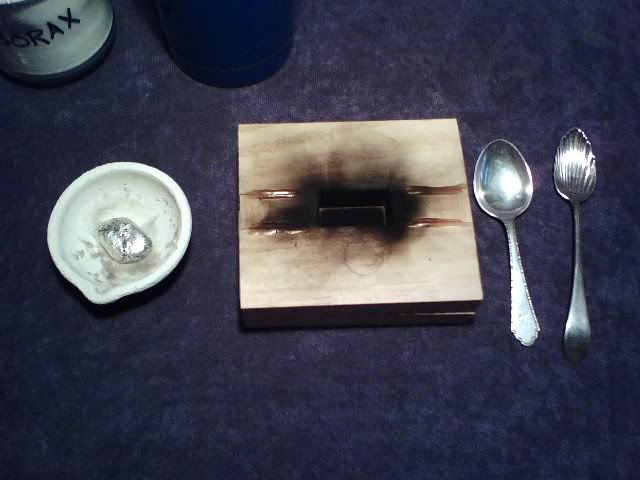
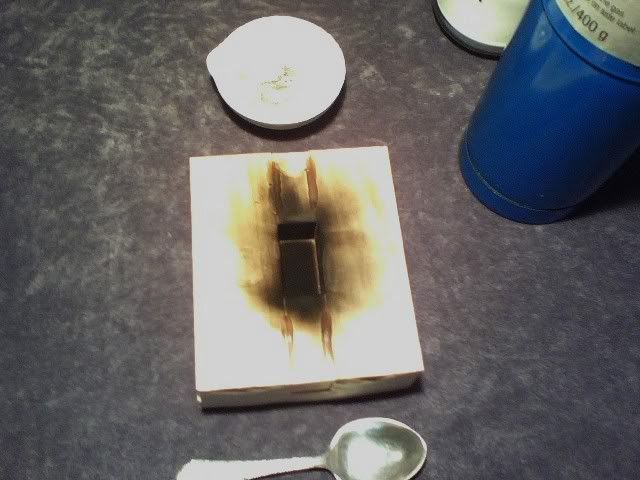